Una mirada lo más amplia posible a un fenómeno digital considerado por muchos la próxima revolución industrial, a través de trece piezas destacadas. Así se imprime en 3D.
Trece ‘highlights’ de la muestra ‘3D. Imprimir el mundo’
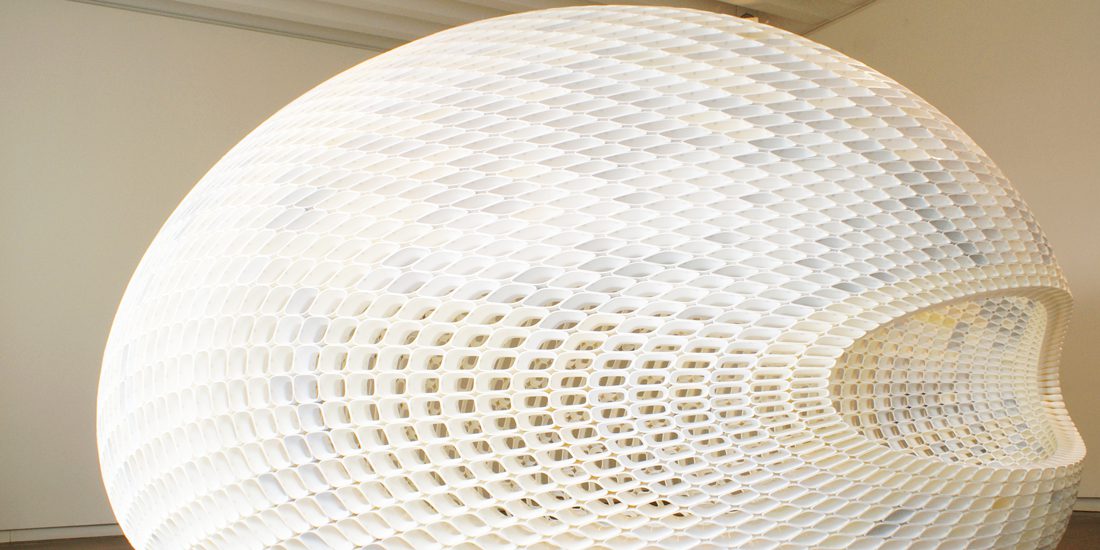
Una mirada lo más amplia posible a un fenómeno digital considerado por muchos la próxima revolución industrial, a través de trece piezas destacadas. Así se imprime en 3D.
Proyecto EGG, 2014. Michiel van der Kley
Esta es la obra de arte colaborativa impresa en 3D más grande del mundo hasta la fecha. Posee 4760 piezas distintas y trabajaron en ella cientos de personas de todo el mundo a lo largo de todo un año. Su objetivo es demostrar las posibilidades de la impresión en 3D desde otro punto de vista: la colaboración a un nuevo nivel y la creación de objetos reales que son, además, piezas únicas.
Top y falda, 2016. Danit Peleg
La primera colección de moda impresa enteramente en 3D mediante impresoras de sobremesa que pueden utilizarse en casa. La colección de Peleg ha sido objeto de atención en todo el mundo, tanto en el sector de la moda como en el tecnológico. La diseñadora se declara convencida de que los avances en impresión 3D revolucionarán el diseño de moda y los procesos de manufactura.
Réplica de Stradivarius impresa en 3D, 2013. EOS
Aunque parece de madera, este violín en realidad está construido con un polímero industrial resistente a altas temperaturas llamado EOS PEEK HP3, utilizado habitualmente en instrumentación médica y material aeroespacial.
«Nuestra tecnología resulta ideal para la creación de estructuras complejas, pero queríamos ponerla a prueba. Por eso elegimos un instrumento musical tan complejo como este», declararon fuentes de EOS a la edición británica de Wired. Algunas piezas, como las cuerdas, el clavijero o los afinadores, fueron creadas por métodos convencionales y añadidas por un lutier, una vez finalizado el cuerpo del instrumento.
Bisagra topológicamente optimizada, 2013. EOS en colaboración con Airbus Group Innovations
El diseño optimizado de esta bisagra para carenados de motor permitió a Airbus Group SE demostrar la ventaja de reducir unos 10 kg por avión (un peso reseñable en el diseño aeronáutico, donde cada gramo cuenta). Gracias a esta optimización en el diseño, la emisión de CO2 se redujo en casi un 40 % a lo largo de todo el ciclo de vida de las bisagras y el consumo de materias primas descendió en un 25 % en comparación con el moldeo rápido por inversión.
Proyecto Daniel, 2013. Mick Ebeling, Not Impossible Labs
Mick Ebeling ha regresado a su país tras crear en Sudán, en plenos montes Nuba, en Sudán, el quizá primer laboratorio y centro de formación especializado en prótesis impresas en 3D. Mick devolvió la esperanza y la autonomía a un adolescente que a los 14 años perdió ambos brazos en una explosión y quería quitarse la vida. El 11 de noviembre de 2013, ese niño recibió la versión 1.0 de su brazo izquierdo. La mano del proyecto Daniel le permitió comer sin ayuda tras dos años (y decidió aprovechar la ocasión para probar por primera vez el chocolate).
Urban Cabin (maqueta a escala 1:20), 2015. DUS Architects / Actual
Este trabajo se deriva del proyecto de impresión en 3D Canal House. Se trata de un espacio de retiro pensado para huir del ajetreo de la vida urbana y está impreso en 3D en su totalidad.
El proyecto buscaba transformar un área industrial abandonada de Ámsterdam en espacio urbano, al que no faltan el miniparque o la bañera al aire libre, y se enmarca en un estudio sobre soluciones de habitabilidad compactas y sostenibles para la ciudad. Para su fabricación se utilizó bioplástico totalmente reciclable que puede almacenarse para reimprimir la cabaña más adelante.
Coche de juguete, 2008. Wouter Scheublin en colaboración con la Organización Neerlandesa para la Investigación Científica Aplicada TNO
Scheublin aceptó el reto de imprimir en 3D y en una única pieza el mecanismo completo de un coche de juguete. Los ejes, las ruedas, el engranaje e incluso los muelles fueron impresos de una sola vez, de manera que las piezas no necesitan ser ensambladas (a excepción de los cuatro neumáticos, hechos de goma). El diseño deja a la vista el engranaje y permite ver cómo funciona el fascinante mecanismo de cuerda.
Polimino, 2015. José Sánchez para Stratasys
Esta serie de piezas impresas en 3D, que pueden combinarse de diferentes maneras mediante imanes para construir una especie de «molécula», bebe de videojuegos como Tetris. «La amplia paleta de color disponible para la impresora 3D Stratasys J750 ha sido fundamental para llevar a cabo el proyecto.
La obra se sirve del color como guía de construcción y solo posee dos geometrías, así que nos servimos del color para diferenciar las piezas conectadas», explica Sánchez.
Kafka, 2012. Neri Oxman para Stratasys
Esta obra parece estar compuesta por diversas partes de animales. En primer lugar, se distingue una columna vertebral humana impresa en un material gomoso proporciona a la vez apoyo y flexibilidad. Envuelve a esta un caparazón-torso, armadura protectora que ofrece además sostén a una serie de elementos semiflexibles (como el cuello en el cuerpo humano). La ornamentada superficie tiene una textura suave y sigue las curvas de la armadura. En las zonas donde la curvatura es mayor (entre las vértebras, por ejemplo) el patrón decorativo es más denso. Nos encontramos ante el interior blando de un insecto combinado con una armadura humana y el pelaje semirrígido de un leopardo: el resultado es este «torso quimérico» de la serie Bestiary («Bestiario»).
Zapatillas deportivas BioKnit, 2015. Ammo Liao
Liao creó las zapatillas Bio-Knit para intentar paliar el problema de exceso de residuos en el sector del material deportivo. Imitando sistemas orgánicos, el diseñador desarrolló un material único y multifuncional que puede presentar texturas suaves o ásperas y ser flexible y sólido a la vez. Los productos creados con este material podrían tener un efecto importante en los procesos de fabricación y reciclado en el sector del material deportivo, pero también en otros muchos. Algunas de sus ventajas más evidentes son la preservación de los recursos naturales, el ahorro de energía, la reducción de residuos sólidos, contaminación y emisión de gases de efecto invernadero. Todo ello gracias a la eliminación de procesos de fabricación innecesarios y a una drástica reducción del coste del reciclado.
Silla sólida C1, 2005. Patrick Jouin para MGX by Materialise
«Cuando diseño un objeto […] siempre hay alguien que me dice: “Disculpa, no puedes hacer esto porque nuestra máquina es capaz”. Así que tengo que cambiar el diseño, aunque no quiera, y encontrar una solución. Otras veces, es el fabricante quien dice: “No puedo vender esto, el mercado no lo aceptará”. En este proyecto, sin embargo, no hay restricciones técnicas ni intermediarios. Es una idea pura. Cruda, sin cocinar. Por eso tiene este aspecto tan increíble». Así explicaba Patrick Jouin su descubrimiento de la estereolitografía (Laurel Saville, Design Secrets, Furniture, 2005). La silla C1 está hecha de resina epoxi polimerizada mediante estereolitografía y sinterización de poliamida pulverizada (nylon).
Esta silla se fabricó mediante una técnica denominada estereolitografía, una especie de impresión 3D en la que un láser controlado por ordenador calienta y solidifica una resina epoxi fotosensible. Esta técnica permite construir, capa a capa, objetos únicos y completos, y difiere enormemente de la artesanía tradicional o la producción en cadena convencional (montaje, moldeo, talla, etcétera).
Taburete One Shot, 2006. Patrick Jouin para MGX by Materialise
Todas las piezas móviles de este diseño son creadas a partir de poliamidas (nylon) en un único proceso de sinterización láser y prototipado rápido. El taburete emerge de la impresora de una pieza, sin necesidad de ensamblaje. One Shot solo puede fabricarse por impresión 3D y se pliega como un paraguas con solo accionar un mecanismo situado bajo el asiento.
Castillo de juguete modular, 2016. Creative Tools
Este proyecto aprovecha el potencial de la impresión 3D en la fabricación de juguetes caseros. El hardware avanza cada vez más rápido, y el tradicional consumo de este tipo de productos puede verse afectado por la rápida adopción de herramientas como las impresoras 3D o el software de modelado 3D. Cualquiera puede ya crear y producir lo que necesite o desee en casa: las modernas herramientas digitales, las licencias Creative Commons e Internet como plataforma de distribución han dado paso a una nueva era. Este proyecto tiene como objetivo demostrar que cualquier persona puede concebir, diseñar, distribuir y personalizar juguetes divertidos desde su casa, usando herramientas 3D e Internet.
‘3D. Imprimir el mundo’, una exposición comisariada por los diseñadores Carmen Baselga y Héctor Serrano, podrá disfrutarse del 15 de junio hasta el 22 de octubre en la planta 4ª de Espacio Fundación Telefónica